The Importance of Wires and Fluxes in Submerged Arc Welding (SAW)
Submerged Arc Welding (SAW) is widely used in industrial applications that demand high productivity, consistent quality, and efficiency. In this process, consumables such as wires and fluxes play a crucial role in ensuring the desired results. In this article, we explore the characteristics and importance of these components and how they can be optimized for different applications.
The Role of Wires in SAW
Wires used in submerged arc welding are responsible for depositing weld metal and forming the weld bead. They are available in various types and chemical compositions, which must be selected based on the base material and project specifications.
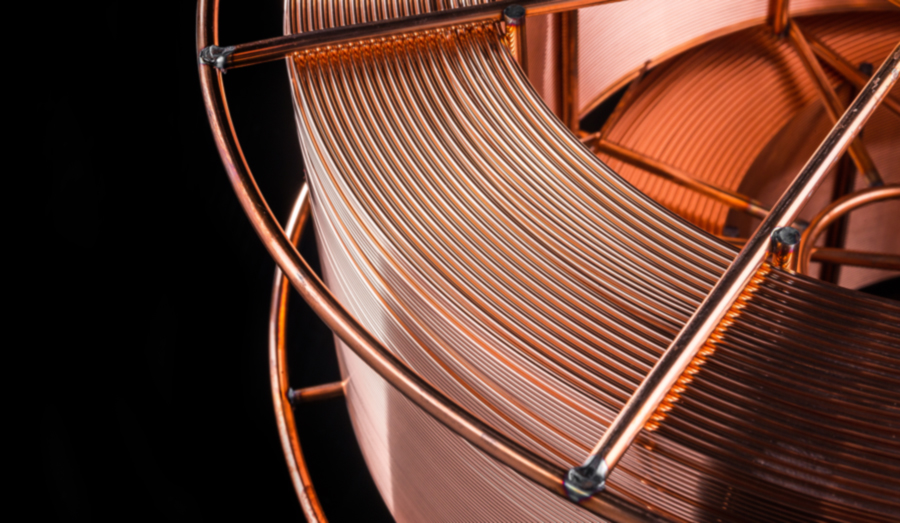
Common Types of Wires:
- Carbon Steel Wires: Used for welding common materials such as structural steel and pipelines.
- Stainless Steel Wires: Ideal for applications requiring resistance to corrosion and high temperatures.
- Low-Alloy Wires: Recommended for welding in extreme conditions, such as cold environments or high mechanical demands.
Factors to Consider When Selecting a Wire:
- Compatibility with the Base Material: The chemical composition must ensure uniform and strong welds.
- Wire Diameter: Depending on the thickness of the material being welded and the welding parameters.
- Performance Requirements: Properties such as crack resistance, ductility, and surface finish.
The Critical Role of Flux in SAW
Flux is a granular material that covers the electric arc and the weld pool during welding, providing protection from external contaminants and directly influencing the quality of the weld bead.
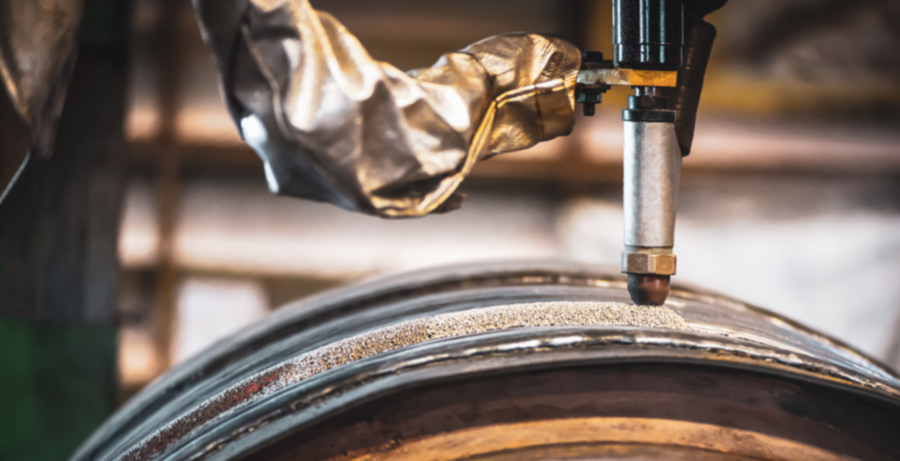
Benefits of Flux:
- Weld Pool Protection: Prevents porosity formation and improves weld integrity.
- Arc Stability: Ensures a consistent process and reduces spatter.
- Adjusting Chemical Composition: Can add elements to the weld bead to meet technical specifications.
The Synergy Between Wire and Flux
To achieve the best results, the combination of wire and flux must be carefully selected. Some fluxes are specifically designed to work with certain types of wires, maximizing productivity and ensuring optimal mechanical and metallurgical properties.
Technological Advances and Sustainability
With a growing focus on sustainability and efficiency, wire and flux manufacturers have invested in solutions that reduce waste and environmental impact. For example:
- Recyclable Fluxes: Reduce material consumption.
- High-Efficiency Wires: Minimize energy consumption.
Electrex’s Commitment
At Electrex, we offer a complete range of wires and fluxes for submerged arc welding, designed to meet the demands of the most challenging markets. We work closely with our customers to identify the best solutions for each application, ensuring quality, efficiency, and performance.
Conclusion
Wires and fluxes are critical components for the success of submerged arc welding. With the right selection and the support of specialists, it is possible to optimize processes, increase productivity, and guarantee high-quality welds. Get in touch with Electrex and discover how we can contribute to the success of your next SAW project!
Discover our offer for welding consumables where you can find our range of wire and flux for submerged arc welding by clicking here!