Category: Technical articles
The Importance of Wires and Fluxes in Submerged Arc Welding (SAW)
Submerged Arc Welding (SAW) is widely used in industrial applications that demand high productivity, consistent quality, and efficiency. In this process, consumables such as wires and fluxes play a crucial role in ensuring the desired results. In this article, we explore the characteristics and importance of these components and how they can be optimized for different applications.
The Role of Wires in SAW
Wires used in submerged arc welding are responsible for depositing weld metal and forming the weld bead. They are available in various types and chemical compositions, which must be selected based on the base material and project specifications.
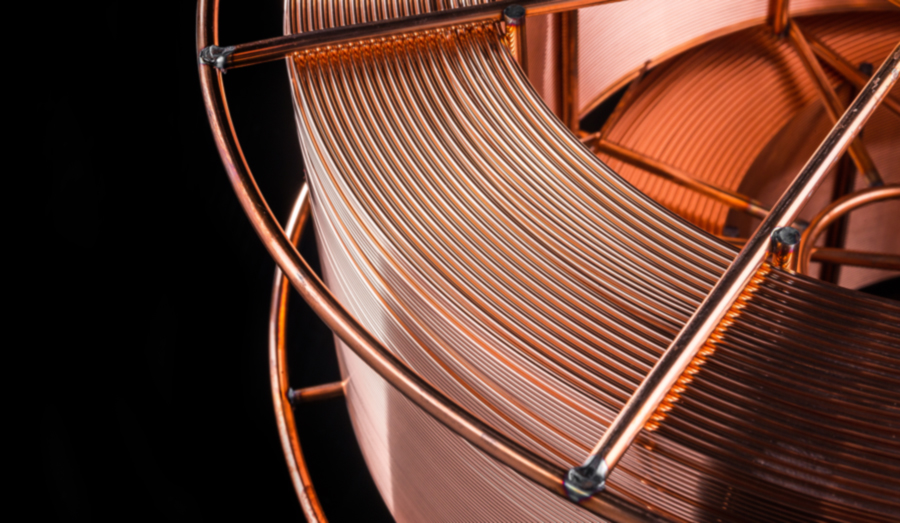
Common Types of Wires:
- Carbon Steel Wires: Used for welding common materials such as structural steel and pipelines.
- Stainless Steel Wires: Ideal for applications requiring resistance to corrosion and high temperatures.
- Low-Alloy Wires: Recommended for welding in extreme conditions, such as cold environments or high mechanical demands.
Factors to Consider When Selecting a Wire:
- Compatibility with the Base Material: The chemical composition must ensure uniform and strong welds.
- Wire Diameter: Depending on the thickness of the material being welded and the welding parameters.
- Performance Requirements: Properties such as crack resistance, ductility, and surface finish.
The Critical Role of Flux in SAW
Flux is a granular material that covers the electric arc and the weld pool during welding, providing protection from external contaminants and directly influencing the quality of the weld bead.
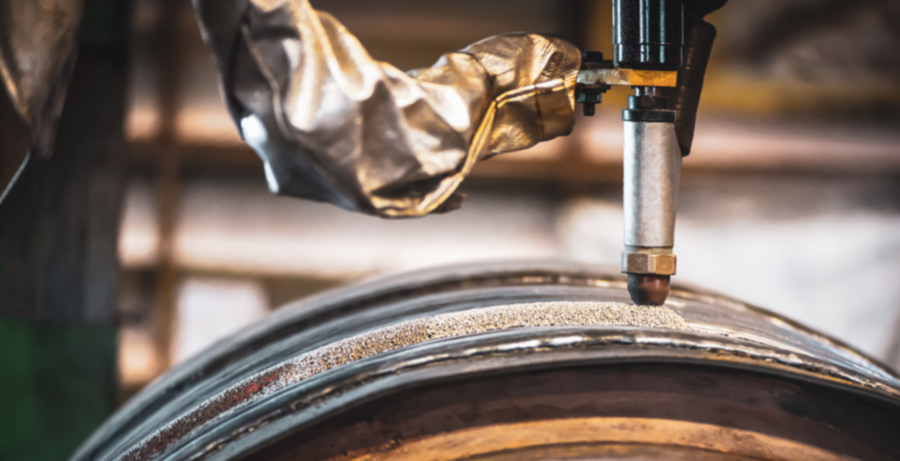
Benefits of Flux:
- Weld Pool Protection: Prevents porosity formation and improves weld integrity.
- Arc Stability: Ensures a consistent process and reduces spatter.
- Adjusting Chemical Composition: Can add elements to the weld bead to meet technical specifications.
The Synergy Between Wire and Flux
To achieve the best results, the combination of wire and flux must be carefully selected. Some fluxes are specifically designed to work with certain types of wires, maximizing productivity and ensuring optimal mechanical and metallurgical properties.
Technological Advances and Sustainability
With a growing focus on sustainability and efficiency, wire and flux manufacturers have invested in solutions that reduce waste and environmental impact. For example:
- Recyclable Fluxes: Reduce material consumption.
- High-Efficiency Wires: Minimize energy consumption.
Electrex’s Commitment
At Electrex, we offer a complete range of wires and fluxes for submerged arc welding, designed to meet the demands of the most challenging markets. We work closely with our customers to identify the best solutions for each application, ensuring quality, efficiency, and performance.
Conclusion
Wires and fluxes are critical components for the success of submerged arc welding. With the right selection and the support of specialists, it is possible to optimize processes, increase productivity, and guarantee high-quality welds. Get in touch with Electrex and discover how we can contribute to the success of your next SAW project!
Discover our offer for welding consumables where you can find our range of wire and flux for submerged arc welding by clicking here!
What’s new in TP AC/DC version 2?
The new version 2 AC/DC TIG welding machines are improved and equipped with several new functions. This article describes what’s new in version 2 compared to version 1 and guides you through some important adjustments you should make to get a better experience with these machines.
New features:
DYNAMICS
This function has been available in TP DC series and is now also available in TP AC/DC version 2. In TIG welding, it allows constant thermal delivery and can in certain cases be an aid to welders who do not have a trained “hand”. You can see a demonstration of this feature in this video:
PULSED MMA
Also available in the TP DC series and now in the TP AC/DC version 2, in this function, the current oscillates between two values (peak current and base current). Applications for this type of coated electrode welding vary, ranging from vertical up and overhead welding to less deformation on thin plates, greater arc control and better welding on gap plates.
TIG SPOT
The TIG SPOT function allows for maximum repeatability and perfection when making points with TIG welding. Set your TIG cycle, adjust spot time from 0.1 to 20 seconds and make perfect, and uniform points.
MANUAL PULSE
When the machine is set to 4T and non-pulsed TIG welding, the operator can switch between main current and base current and so on by quickly pressing and releasing the torch trigger.
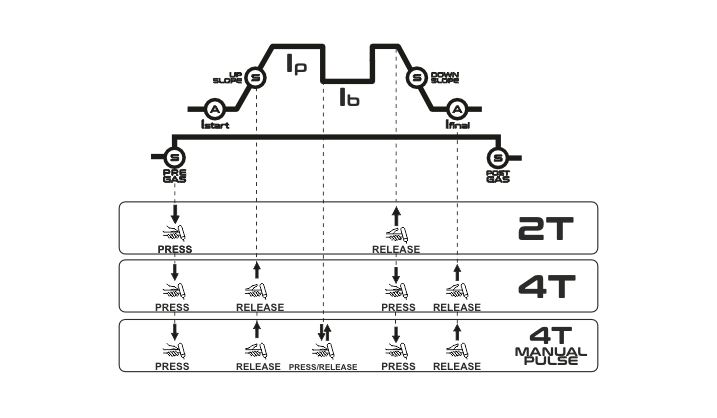
JOBS
The JOBS function, memories to save and repeat your welding programs, is not new in version 2, but it has gone from 9 available memories (version 1) to 20 (version 2), allowing the operator to have more room for maneuver.
ARC IGNITION
TIG arc ignition has been improved in version 2. To optimize arc ignition, the operator will have to define the tungsten electrode thickness in advance. It is an important adjustment that will greatly affect the quality of the welding work. Therefore, we transcribe a part of the instruction manual:
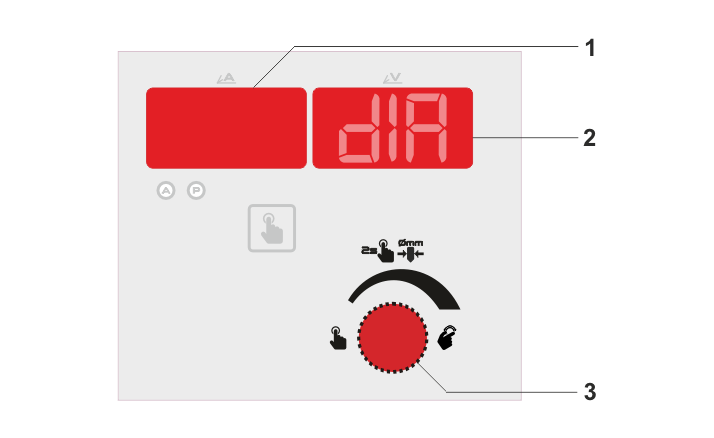
– Press button 3 for 2 seconds until display 2 shows dIA. Turn knob 3 to select the appropriate tungsten electrode diameter (values 1.0, 1.6, 2.4, 3.2 or 4.0 mm are shown on display 1).
ERROR 6
In version 2, a new error was introduced (Er6) where the machine automatically detects the lack of phase of a certain electrical installation and alerts the operator.
These are the main features that the user must consider in their welds. In addition, the machine has been improved and optimized internally, namely in the high-frequency module and in the control module.
Comparison of Electrex MIG/MAG welding machines
Electrex has several and different options when it comes to MIG/MAG welding machines: Inverter or conventional power source? Electronic or step control? Standard or pulsed? And we could continue with more options. In this article we try to clarify the different lines of Electrex MIG/MAG welding machines: DIGIT II, SYNERGIC II, LTRONIC SYNERGIC, MULTI BASIC and MULTI PULSE.
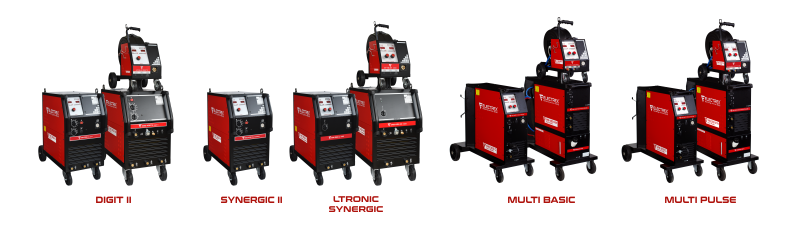
The most striking difference is the type of power source. The DIGIT II, SYNERGIC II and LTRONIC SYNERGIC lines are based on transformers and the MULTI BASIC and MULTI PULSE lines are with inverter technology. Transformer-based ones allow them to be more accessible in terms of purchase price, but at the same time have more weight and volume, while inverters allow for better energy consumption, low weight and compact design.
Regarding the control, on the DIGIT II and SYNERGIC II the welding voltage regulation is carried out by switches, and the regulation is stepwise. On LTRONIC SYNERGIC, the welding voltage is regulated by thyristors, allowing for continuous adjustment. Finally, on MULTI BASIC and MULTI PULSE, just like LTRONIC SYNERGIC, regulation is carried out electronically, but these through modulation of transistors switching. This allows for a more stable and accurate welding arc.
DIGIT II, SYNERGIC II and LTRONIC SYNERGIC welding machines only allow one welding process, ie they only allow MIG/MAG welding. As the name implies, MULTI BASIC and MULTI PULSE allow, in addition to the MIG/MAG process, coated electrode welding (MMA) and TIG welding (with contact ignition). Therefore, they are multi-process.
SYNERGIC II, LTRONIC SYNERGIC and MULTI PULSE allow welding using synergistic programs, ie welding programs adjusted at the factory and optimized for different metals such as steel, stainless steel and aluminum.
Regarding pulsed MIG/MAG welding, only the MULTI PULSE line offers this type of welding, which is a variant of MIG/MAG, allowing for thin plate welding, almost without projections and out-of-position welding.
Discover our MIG/MAG welding machine lines:
Basic Questions Before Buying a Welding Machine
What material to be welded?
In addition to your experience or the learning curve for each welding process, the metal to be welded will greatly affect the welding machine you will buy, as each machine will only have specific welding processes available*.
Here is a table of the metals to be welded and the respective welding processes you can use:
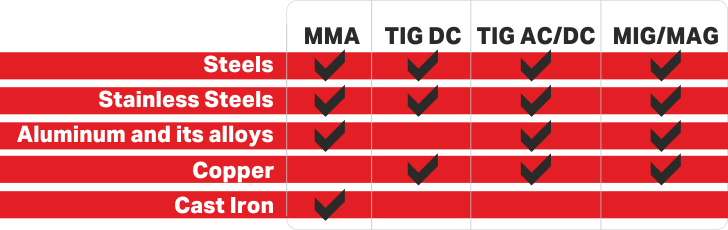
Within the TIG, we distinguish the DC TIG and AC/DC TIG variants, because it is only possible to weld aluminum and other light alloys with the AC TIG variant (TIG in alternating current).
*Note: there are machines with more than one welding process available. These are the multi-process.
Machine power supply?
To buy a welding machine, you need to know what type of supply voltage is available at the place where you are going to weld. If you go to DIY jobs at home, you will probably only have single-phase electricity. If it is in a company, you will also have the option of three-phase voltage (usually 380 or 400V). Be careful when buying from foreign sites, as there are machines prepared for other voltages that are not available in your country.
What is the place where you are going to weld?
It may seem like a secondary aspect, but the place where you are going to weld is very important when choosing your welding machine. For example, if you go outdoors, in a location with wind, the best options are stick welding machines (coated electrode). In this welding process, unlike MIG and TIG, the electrode already has gas protection in its coating so that the wind will not compromise the quality of your welds.
Where you are going to weld can also influence the type of design of the welding machine. To weld in a place where there are obstacles (for example, a shipbuilding workshop or a civil construction work), your machine must have portability and mobility, allowing the welder to transport it from place to place. In this case, in addition to compact and light machines, MIG/MAG machines with a separate feeder are good options.
Long or short weld beads? Thick or thin materials?
The length of your welds and the thickness of the workpieces to be welded will influence the current range and duty cycle that your machine will need to have. The current range will depend on the thickness of the metal to be welded, so the thicker it is, the more power the welding machine will have to have. The machine’s duty cycle will comprise how long you will be welding at a given amperage or welding current. For example: if the machine specifications states that the welding current is 200A – 60% and 160A – 100%, it means that the welding machine will weld for 6 minutes with a welding current of 200 Amperes and with a current 160 amps can run continuously. After this time of 6 minutes, the machine will probably turn on the thermal protection so you will have to let it cool down. The current range and its duty cycles must be considered and are a good comparison between different brands of welding machines.
Machine’s price?
The budget you have available for your new welding machine is a subjective matter and no longer depends on the factors described above. Remember that after-sales service, machine durability and welding results must also be considered and that they often require higher investments, which pay off in the long term.
TIG pulsed welding
TIG pulsed arc welding is a variation of the TIG process, which switches between two levels: a peak current and a base current. Although this variant existed for several years, nowadays with electronic power control technologies we can achieve pulses per second (pulse frequency) much higher than those of a machine with conventional technology. For this, we need an inverter welding machine with pulsed Tig as such of the Electrex’s TP range (163, 203, 223, 253, 323, 403, 503 DC ou AC/DC).
PULSED TIG ADVANTAGES

This process allows the incensement of the quality of the welds, it reduces the costs of the process, obtaining narrower or wider arcs, it controls the temperature of the welding bath, it allows welding with more or less penetration or even reproduce the dimes effect more easily.
Besides these, allows:
- less heat input to the work piece, preventing the deformation of the work piece.
- an arc more concentrated, allowing more penetration.
- possibility of welding plates of different thicknesses
- More control of the welding bath.
PULSED TIG ADJUSTING PARAMETERS

Take the example of ELECTREX TP 323, for regulating the pulsed parameters and its consequences in the welding process.
After selecting process of TIG welding and pulsed mode, we have 4 specific parameters that can regulate pulsed TIG:
Main Current (Amperes), the base current (Ampere), pulse frequency (Hz) and peak current ratio time / Base current time (%).
The main current or peak current is the current with higher intensity, while the base current is the current at a lower intensity. The welding current value is the average of the two currents levels.
The pulsed rate is represented by the number of cycles per second between 0.5 and 200 cycles per second.
At a higher pulse rate corresponds to a more concentrated arc, producing narrower seams and decreasing the thermally affected zone.
The cadence of the dimes effect will also be proportional to the pulse frequency and a smooth seam with a very high pulse rate can also be obtained.
Finally, the pulse time or length can be adjusted at both current levels and the effects of pulse length identical to pulse rate can be adjusted.
The shorter the main current time, the lower the heat induction, there will be greater penetration and narrower seams will be obtained.
Wave forms AC welding
The old TIG machines with conventional technology used the sinusoidal waveform in TIG welding in alternating current (AC). Nowadays, the new inverter TIG AC/DC machines allow the selection of various waveforms in TIG welding in alternating current (AC). This selection, without changing other parameters of welding, allows to change the characteristics of the arc, the seam, and the cleaning / penetration effect.
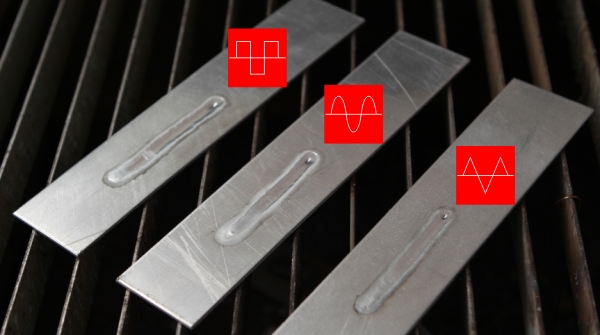
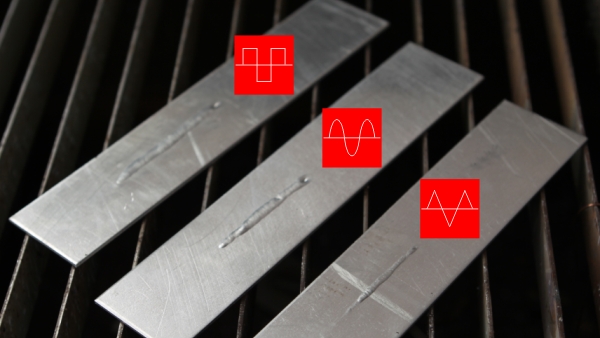
Square wave:

Welding of light alloys with more penetration into thick plates. It forms a more “strong” arc, then more rough and noisy, where there is more heat transfer. It forms a broader and thicker seam.
Sine wave:

Is used in most applications.
The arc is smoother and less noisy than the square wave.
Triangular wave:

Welding of thin plates with little transference energy and thus, less penetration. It reduces the distortion of the parts and allows a fast solidification of the welding bath. It is especially recommended for thin-thickness aluminum.
Weding Visual Inspection
There are many ways to inspect a weld, but one of the simplest, practical to do, is the visual inspection. This is surely a non-destructive testing, which lets you monitor what is happening on the surface with the naked eye or through a magnifying glass. There are other techniques such as radiographic testing or ultrasound testing, which should be part of the quality proceedings. The weld bead, its shape and form, is a major defect indicator in a weld, but not the only: the heat-affected zone, the presence of projections, cracks or distortions in the workpiece, among others are also indicators of welding quality. The most common defects in a weld joint may be due to the following causes:

Falta de penetração
– corrente ou velocidade de soldadura muito baixas
– abertura excessiva da junta
– chanfro inadequado
– grande espessura da peça de trabalho
– distância excessiva entre o eléctrodo e a peça de trabalho
– posição ou movimento do eléctrodo inadequados
– diâmetro do eléctrodo inadequado

Mordedura:
– corrente ou velocidade de soldadura demasiado elevadas

Preparação incorrecta da junta:
– chanfro inadequado
– desalinhamento das peças a soldar

Fissuras:
– Crateras no final da soldadura
– tipo de eléctrodo inadequado
– eléctrodo húmido
– grande espessura da peça de trabalho
– chanfro incorrecto

Excesso de respingos:
– corrente de soldadura muito elevada
– grande distância entre eléctrodo e a peça de trabalho
– peça suja- eléctrodo húmido

Inclusão de escória:
– escória não removida durante passes ou na troca de eléctrodo
– posição ou ângulo de eléctrodos inadequados
– diâmetro do eléctrodo muito elevado ou chanfro muito estreito

Porosidade:
– Peça suja, enferrujada ou húmida
– corrente de soldadura incorrecta
– velocidade de soldadura elevada
– distância excessiva entre o eléctrodo e a peça de trabalho
– eléctrodo húmido

Distorção de contracção e angular:
– corrente ou velocidade de soldadura demasiado elevadas